Automatisation de la plonge : moins de pénibilité, plus d’efficacité
- Temps de lecture : 5 min
Les dernières technologies développées par les fabricants de lave-vaisselle pour le CHR s’orientent sur l’automatisation, afin de réduire la pénibilité du travail à la plonge et de diminuer son impact sur l’environnement. Zoom sur des appareils qui brillent d’ingéniosité.
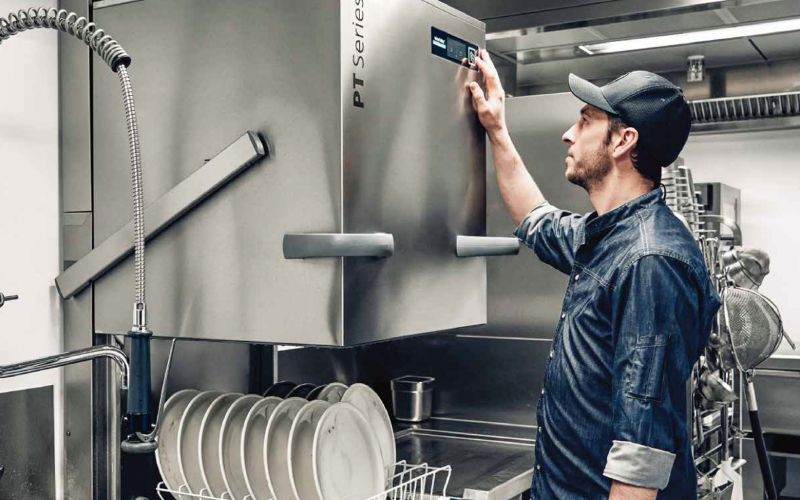
La plonge… un poste souvent délaissé, sur lequel on ne se précipite pas pour investir. C’est pourtant un rouage primordial qui pâtit d’une mauvaise image et de salaires peu attractifs pour un travail le plus souvent pénible. Résultat : c’est l’un des postes qui connaît le plus de turn-over et d’absentéisme. À force de recrutements de dernière minute et d’heures perdues, la question du matériel finit généralement par se poser.
Les machines récemment mises sur le marché répondent ainsi en priorité au besoin de diminuer la pénibilité du travail, en automatisant nombre de manipulations, à commencer par le relevage des machines à capot. Meiko avait lancé les hostilités en 2018 avec sa laveuse à capot M-iClean H intégralement automatisée. Les manipulations sont réduites au minimum, le capot se referme automatiquement dès qu’un casier est détecté et s’ouvre de la même façon à la fin du lavage. Un écran à gauche de la machine permet à l’opérateur de la commander sans se déplacer. À la clé, plus de confort puisqu’il n’a plus à actionner la barre de relevage et un gain de productivité. De plus, la surveillance du cycle de lavage n’est pas nécessaire, ce qui lui permet de voguer à d’autres préoccupations pendant ce temps.
Consommer moins d’électricité
Trois ans plus tard, Winterhalter vient tout juste de mettre sur le marché sa gamme PT, qui pousse là aussi très loin l’automatisation, aussi bien pour le confort de l’utilisateur que pour un volet désormais tout aussi scruté, celui des économies d’énergie. Pour réduire la pénibilité, un bouton à hauteur de travail dispense de la manipulation du capot (en option). Mais sur le volet des conditions de travail, les gros efforts du fabricant pour diminuer les émissions de buée sont à souligner. En effet, en installant des condenseurs, l’appareil réussit à la fois à limiter l’échappement dans la pièce et à convertir ces calories en énergie de chauffe de l’arrivée d’eau. « Le système aspire la buée en sortie de rinçage – elle est alors entre 60 °C et 85 °C – et la convertit en énergie pour chauffer l’arrivée d’eau », explique Mickaël Mercier, responsable qualité et technique chez Winterhalter. Une version intègre par ailleurs une pompe à chaleur double flux qui recycle non seulement les calories à l’intérieur de la machine, mais aspire également celles de l’air ambiant.
« C’est très utile dans des pièces avec une mauvaise aération, la machine restitue de l’air entre 18 °C et 25 °C, ce qui permet d’assainir considérablement l’atmosphère de travail. » L’eau de la cuve (60 °C) est revalorisée de la même manière, pour le préchauffage mais aussi pour les appareils équipés d’une pompe à chaleur, pour chauffer la cuve. La consommation d’électricité est dans ce cas nulle. Concernant le séchage aussi, les calories de lavage sont optimisées.
« Nos appareils n’intègrent pas de fonction de séchage. En sortant de la machine, la vaisselle a emmagasiné des calories, de l’ordre de 65 °C et le choc thermique à l’ouverture du capot suffit au séchage. » Au final, le fabricant revendique une machine à capot « qui ne consomme pas plus qu’un lave-verres », à savoir 7,9 kW.
Sans essuyage
Parmi les autres acteurs du secteur, la récupération de chaleur fait également partie des axes de développement, que ce soit pour chauffer l’eau d’alimentation – comme c’est le cas sur les machines à capot Elea et G-HR de Comenda avec une économie d’énergie de 35 % sur ce point – ou pour assurer le séchage de la vaisselle en fin de cycle. Hobart, leader du secteur, figure parmi les pionniers sur cette technologie avec son lave-vaisselle Premax, équipé d’un système de ventilation qui génère de la chaleur sèche. Cette technologie Top-Dry, qui permet de ranger la vaisselle sans avoir à l’essuyer, a d’ailleurs permis à la marque de remporter le prix Best of Market en 2019. L’appareil intègre également un module Wifipour le contrôle et l’allumage de la machine à distance, évitant ainsi une mise sous tension trop en amont.
Hobart affiche clairement son objectif de tendre vers un lavage sans eau. Avec le Pre-max, la marque propose un lavage avec un demi-litre d’eau par casier ainsi qu’un capteur du degré de salissure pour adapter la consommation. Sur son dernier-né, le Two-Level-Washer, premier lave-vaisselle à capot du monde à deux niveaux, l’enceinte dédiée au lavage des ustensiles intègre un effet de trempage dans le processus de lavage, ce qui dispense de prélaver la vaisselle. Également, la qualité de l’eau du bain de lavage est mesurée en permanence afin d’ajuster la quantité d’eau de rinçage au minimum, pour une économie jusqu’à 2 litres par cycle.
Les machines dotées de systèmes efficaces de récupération des déchets ont aussi une portée écologique dans la mesure où elles évitent le prérinçage à la douchette et permettent de doser plus modestement la quantité de détergent et d’eau de rinçage nécessaire. Sur sa gamme PT, Winterhalter intègre un détecteur du degré de salissure permettant d’adapter automatiquement l’intensité du cycle, et donc la quantité d’eau et de produit nécessaires. En outre, les champs de lavage ont été redimensionnés en forme de « s » pour favoriser une meilleure répartition de l’eau dans l’enceinte, et couplés avec une rotation motorisée, « cela permet d’économiser 0,4 l lors de la phase de rinçage ». À force de réduire les consommations, l’effet domino vertueux engagé par les fabricants – moins d’eau, moins d’électricité et de fait moins de produit lessiviel – devrait considérablement modifier le poste de plonge et peut-être même, l’image du métier.
La Comenda Duo incite à passer aux bouteilles en verre
Comenda fait dans l’écologique par ricochet en dévoilant le lave-vaisselle Duo doté d’un cycle spécifique pour le lavage des bouteilles et carafes en verre. En plus des paniers à vaisselle, la machine dispose d’un panier adapté pour les carafes, doté de capteurs et de buses qui activent un circuit hydraulique séparé pour nettoyer correctement l’intérieur des bouteilles avec une eau à 85 °C. La solution peut accueillir des bouteilles jusqu’à 35 cm de haut et d’un diamètre de 10,6 cm au maximum.